Use of propane as refrigerant in process chillers
Long term refrigerant solution
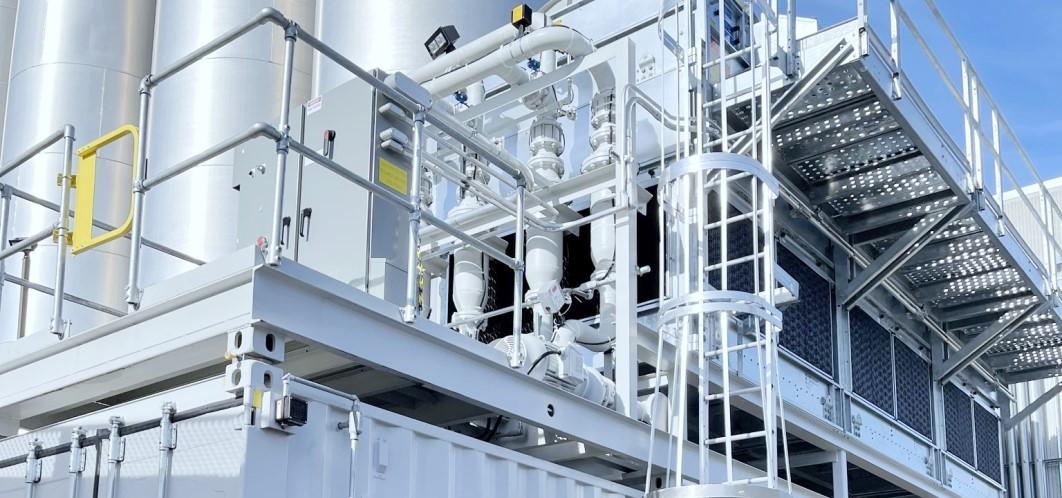
A case study of an R290 retrofit from R22 for a plastic film extrusion manufacturer.
A plastic extrusion film and sheet production company recently decided to revamp their process chilling system to be in line with their corporate guidelines for environmental responsibility and sustainability in all facets for their operations.
The company regularly evaluates the usage of energy and raw material consumption throughout the production process and organization. Driven by the spirit of saving resources and protecting the environment, they incorporate energy recycling and the use of recyclable materials in their manufacturing processes. With this mind, they decided to replace their existing process chilling system with one utilizing a long-term and environmentally friendly refrigerant.
“The design of a new production cooling process chiller, with the aim of lowering the direct and indirect emission to the atmosphere by reducing the process power consumption and using a low GWP refrigerant was the challenge handed to us by the customer.” - said Edward George, Director of Sales at Budzar Industries.
The project involved the replacement of a 500 ton air-cooled R22 chiller with a system that would provide the desired environmental benefits while also providing a long term solution that would not be subject to potential changes in environmental policy.
Finding a perfect refrigerant is complicated. On top of environmental concerns, chiller manufacturers need to consider safety, compatibility with existing plant equipment, and maintaining/improving efficiency.
“Efficiency is very important as we consider the environmental ramifications of these new refrigerants. If the refrigerant is going to reduce efficiency, we are increasing the carbon footprint significantly even if the GWP of the refrigerant chosen is lower.” Said Matteo Iobbi, Chief Technical Officer at Frascold USA.
The initial evaluation started with a theoretical compressor calculation. Capacity and efficiency comparisons among a certain number of refrigerants was done using only alternatives with a GWP of 10 or less. Propane proved to be the best compromise between the options considered.
Design and Operational Considerations
Being an A3 refrigerant (highly flammable) the propane charge had to be kept as low as possible for the refrigerating capacity needed. The charge also needed be confined and the equipment installed outside.
R290 flammability considerations were handled by our partner Budzar who designed and manufactured a Class 1, Division 2, Group D chiller for outdoor installation. The compressors were easily selected, and performances simulated on the Frascold selection software (FSS3).
The machinery was confined in a containerized machine room with LFL (low flammability level) detectors, explosion proof extraction fans and constant cross air flow. Explosion proof conduit fittings were used, and every enclosure is pressurized above container pressure. The machine room temperature is regulated via heaters and kept at 70 °F.
The chiller has three independent refrigeration circuits, each of them with one Frascold CXH92-300-912 compact screw compressor with integrated oil separator. Because the Frascold CX compressors have high efficiency integrated oil separators the total charge was considerably lower than other possible solutions due to the lack of need for external oil separators.
A secondary fluid (25% glycol) is utilized on the evaporator side and the chiller can deliver a glycol outlet temperature between 35/40°F. Each circuit has its own circulating pump and 70 pounds of R290 with 187 tons of refrigeration capacity, giving a total of 560 tons. Each refrigeration circuit can be individually regulated and controlled for system settings, monitoring, and troubleshooting.
On the condenser side a cooling tower was utilized with three cooling tower loops, each one equipped with a dedicated pump controlled by a VFD. A secondary fluid (25% glycol) was used on the condenser side as well. The ability to keep a saturated discharge temperature of around 105 F on the hottest days of the year guarantees a significant power consumption savings.
In conclusion, we can say that propane is a valid and long-term alternative for process cooling operations in the US market. Smaller footprints and better efficiencies compared to other refrigerants means that propane is attractive both from environmental and economic standpoints. Flammability concerns can be mitigated through engineering, component selection and risk analysis leading to safe and efficient operation.
Frascold offers both reciprocating and screw compressors for Hydrocarbons from 1/2 HP to 310 HP. We have participated in thousands of hydrocarbon installations worldwide and have invested heavily in R&D as well as testing equipment specifically for flammable refrigerants.